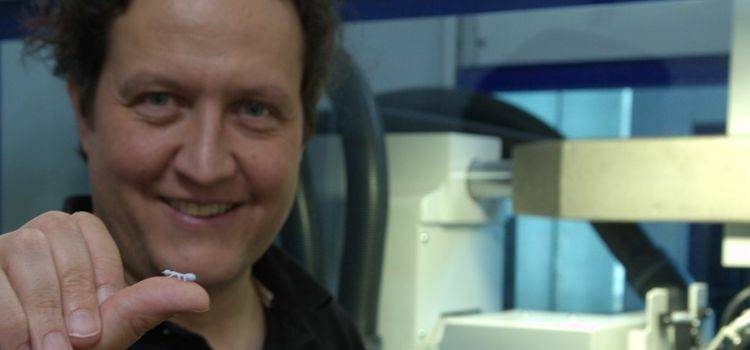
Bioplastic ants
What is the ant project about?
Julia Bugram's ant project is an art project that takes place in public space. Ants made of bioplastics are glued to school paths, squares, etc. with the children to explore public space. So that the ants do not pollute the environment when washing dishes, they are made of bioplastics. This way, no microplastics get into the environment.
What steps are needed from the idea to implementation?
In terms of plastics, three things are required. First, an injection molding machine or micro-injection molding machine, since the ants are very small and delicate. A so-called “tool” is also required for the machine. This is the mold into which the bioplastic is injected and the ants are formed. And last but not least, you also need the appropriate bioplastic material.
What are the production steps?
The bioplastic is heated in the injection molding machine and transported by means of a screw in the direction of the injection molding tool (injection mould). The liquid bioplastic is then injected into the tool, shaped and then cooled directly in the tool. In the last production step, the finished ant is then ejected. In this case, it is a multiple tool that can be used to produce several ants in one operation.
What are the requirements for bioplastics?
Due to the requirements in the production of ants from bioplastics, the bioplastic material consists of a mix of different natural/vegetable raw materials. The ants must be neither too soft nor too hard. The fine antennae must be able to be cast accordingly, but must not break off too easily.
How does the processing differ from petroleum plastic?
In principle, everything that can also be made from petroleum plastic can be made from natural plastic/bioplastic. In processing, the difference lies in the small details. This is primarily about the shrinkage behavior of the material, i.e. the reduction in volume due to cooling, and the processing temperature, since bioplastic behaves somewhat differently than you are used to from conventional plastics. As a result, the manufacturing process must be adjusted accordingly.
What is bioplastic made of?
Bioplastic consists of vegetable raw materials instead of petroleum. This is usually sugar or starch, which is processed accordingly so that it can be processed like plastic.
Can I produce bioplastics myself - are there any experiments?
Just as it happens in the correct production with lactic acid, it cannot be imitated, but in a similar way with the raw materials milk and vinegar. How exactly this works, we will explain to you in detail in this Article on our website.
What advantages do products made of bioplastics offer?
As we can see from this ant project, everything that can be made from conventional plastic can be made from bioplastic. The big advantage of using bioplastics is that plants that grow back and bind CO2 are used as raw materials. Therefore, the CO2 bound in the plastic comes from the atmosphere and not from fossil sources that are harmful to the climate.
At the end of the product lifecycle, products made from bioplastics are compostable and do not break down into microplastics. With all these advantages - why aren't all products made of bioplastics?
The only disadvantage of bioplastic is the higher price. That is why not all petroleum-based plastic products are being replaced by bioplastics.
Why is the ant project particularly exciting?
The ant project is also an opportunity for us to try out special challenges and material compositions. We have already used recycled bioplastics here for the ant. Using recycled bioplastic is also where it needs to go. In the next step, we will also test adding algae to the bioplastic for the ants.
Why does NaKu make ants out of bioplastics?
NaKu generally manufactures special projects from bioplastics for customers. This is the third pillar of NaKu. Here we provide children's toys, special packaging for natural cosmetics and much more. here. By default, NaKu produces foils and bags made of bioplastics as well as bottles and cans made of bioplastics.
Why is NaKu passing on its knowledge of bioplastics to schools, universities, etc.?
We really like working with educational institutions, as this is a very fruitful and creative collaboration. We also like to do start-up projects, where we can help with our bioplastics expertise. For example, a special plant bag made of bioplastics was developed with the Schönbrunn Gardening School for a reforestation project in Kenya. Such projects show that bioplastics make a lot possible, but that it just has to be done.
How is an injection mold made?
The injection mold is milled from a block of metal with a milling cutter. A particularly fine milling tool was required for the ants. The milling process itself is computer controlled and runs on a 3D milling machine. First, the injection mold is drawn on the computer, appropriate software then converts it accordingly for the milling process.
How does the cutter work?
The self-rotating or rotating milling cutter mills the injection mold out of the metal block using forward and downward movements. The deep movement is carried out in several steps.
How fine is the cutter for the injection mold of the ants?
In order to be able to better imagine the fineness and size of the cutter for the ants, we compared it with a human hair. This comparison is best seen in the video.